贝克真空泵在塑胶行业的创新应用:高效节能与精密成型解决方案
在塑胶行业追求高精度、低能耗、绿色化生产的趋势下,真空技术已成为注塑成型、挤出加工、真空镀膜等核心工艺的关键支撑。贝克真空泵凭借干式无油、快速响应、耐高温腐蚀等核心技术,为塑胶制品生产提供全流程真空解决方案,助力企业实现降本增效与工艺升级。
一、塑胶行业核心工艺与真空技术需求
1. 注塑成型:精密脱气与快速循环
- 工艺痛点:
- 模具内气体残留导致产品气泡、缩痕(缺陷率>5%)
- 传统油润滑泵污染液压油,增加维护成本
- 贝克方案:
-干式爪式真空泵:0.5秒快速抽至-0.95bar,脱气效率提升40%
- 无油设计避免污染,模具清洁周期延长3倍
- 智能联锁系统,与注塑机同步启停,节能30%
典型应用案例:
某汽车配件厂采用贝克RA 0025F爪式泵后:
- 保险杠成型周期从55秒缩短至42秒
- 产品表面缺陷率从4.8%降至0.6%
- 年节省液压油更换成本¥12万
2. 挤出成型:高效原料干燥与稳定输送
- 技术挑战:
- 原料含水率>0.02%导致挤出制品开裂
- 高温环境(80-120℃)下真空泵稳定性差
- 贝克方案:
- 耐高温螺杆真空泵:配置陶瓷涂层,持续耐受150℃热风
- 两级真空干燥系统,使原料含水率≤0.005%
- 集成冷凝器回收挥发性有机物(VOC回收率>90%)
客户价值体现:
- 挤出机产量提升25%(消除原料结块堵塞)
- 每吨制品能耗降低18%
3. 吹塑成型:中空制品均匀成型
-行业需求:
- 瓶胚壁厚偏差需<±5%
- 吹塑周期需压缩至10秒以内
-贝克技术突破:
- 涡旋真空泵+气动增压系统:0.3秒达到-0.9bar
- 多点真空吸附夹具,实现复杂曲面均匀成型
- 智能压力补偿算法,消除型坯下垂变形
实测数据:
某PET瓶生产线上:
- 1.5L瓶胚壁厚偏差从7.2%优化至3.5%
- 设备OEE(综合效率)从76%提升至89%
贝克真空泵技术优势对比
性能维度
|
传统液环泵
|
贝克干式真空泵
|
提升效益
|
能耗效率
|
能耗占比25%以上
|
变频控制能耗<18%
|
年电费节省¥50万/台
|
维护成本
|
每月更换密封件/润滑油
|
20,000小时免维护
|
维护费用降低92%
|
洁净度
|
油雾污染制品表面
|
无油运行
|
产品合格率提升4.2%
|
耐温性
|
耐受80℃
|
持续耐温150℃
|
适用场景扩大3倍
|
响应速度
|
抽真空时间>3秒
|
0.5秒达到工作真空度
|
生产效率提升25%
|
特殊工艺场景解决方案
1. 真空镀膜(IMD/IML)
-工艺要求:
- 镀膜真空度≤5×10⁻³ mbar
- 膜层附着力≥4B(ASTM等级)
- 贝克技术方案:
- 罗茨泵+分子泵组合系统,极限真空达10⁻⁴ mbar
- 磁流体密封技术避免轴封漏气
- 某家电面板厂应用后:
- 镀膜良率从88%提升至97%
- 金属膜层厚度均匀性±2nm
2. 热成型(吸塑包装)
- 行业痛点:
- 薄片材料(0.2-0.5mm)吸附易破裂
- 多腔体同步成型效率低
- 贝克创新设计:
- 分布式真空系统,独立控制8个成型工位
- 压力梯度控制技术,避免材料过度拉伸
- 典型案例:
- 快餐盒生产速度从60模次/小时提升至85模次
- 材料损耗率从3.1%降至0.8%
绿色生产与智能化升级
1. 节能降碳技术
- IE4超高能效电机,比传统泵节能35%
- 余热回收模块,将50%废热转化为干燥热能
2. 智能运维系统
- 物联网远程监控:实时监测真空度/温度/振动参数
- AI预测性维护:故障预警准确率>90%
- 某跨国塑胶集团部署后:
- 非计划停机减少70%
- 备件库存成本降低45%
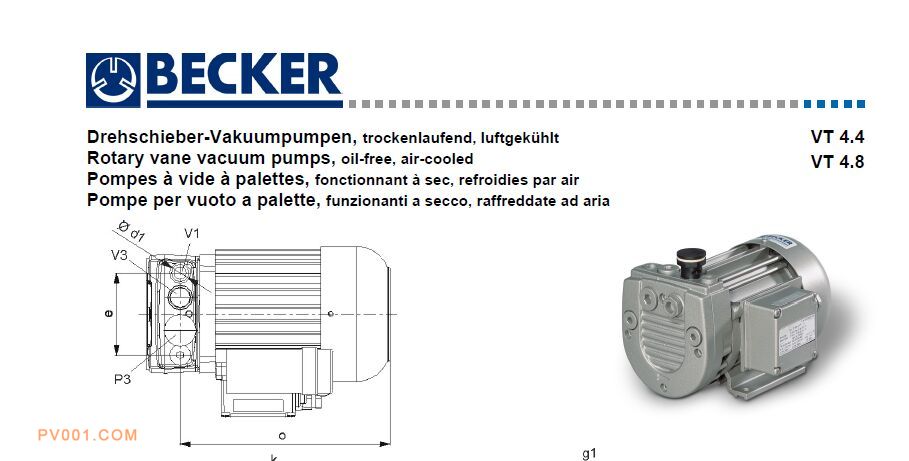
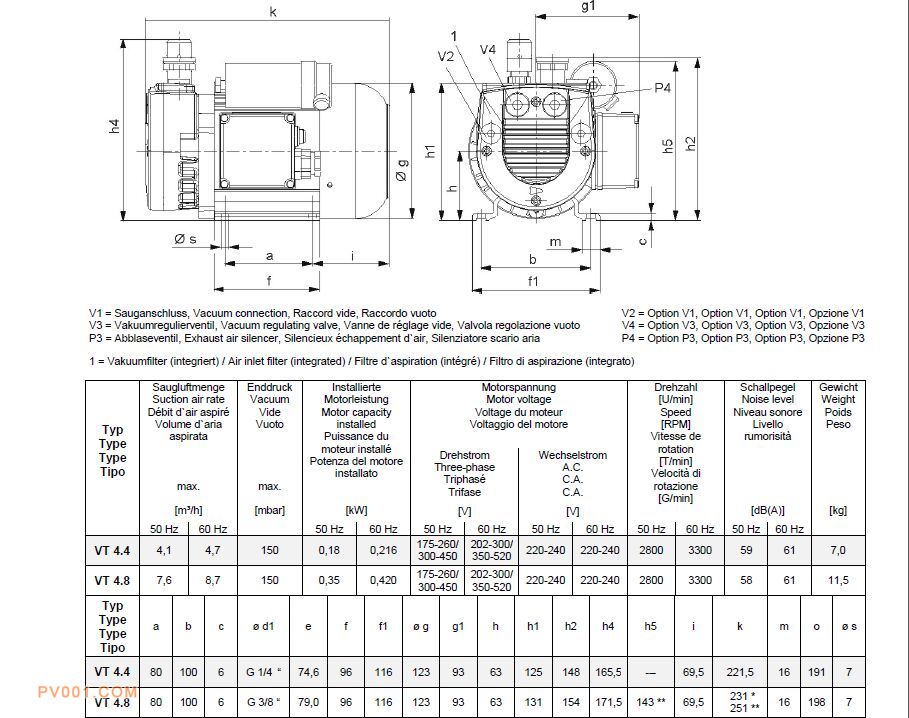
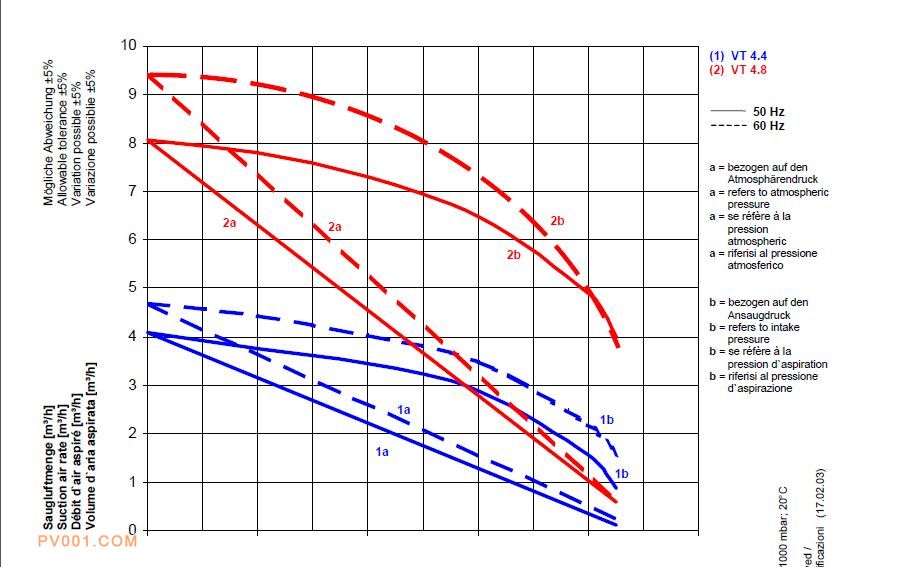